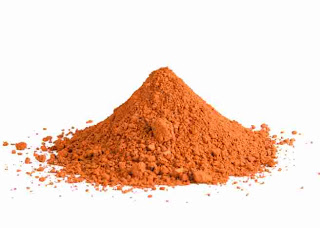
RED PIGMENT Name : Red Earths / Red Ochre
Composition : Iron(III) oxide chromophore (Fe2O3 + clay + silica)
Band Wavenumbersa / cm-1 and Relative Intensities b: 220vs; 286vs; 402m; 491w; 601w
Excitation Wavelength and Power : 632.8 nm 3 mW
Hematite : Hematite has the formulae Fe2O3.
It has a relative hardness of 7.It is the most abundant and important ore or iron.
OCHRES are the natural mineral pigments occurring in various shades and colours, generally ranging from yellow to red to brown. The colouring power is mainly due to oxides of iron. They are also called 'coloured earths'. Ochre is a colouring mineral. The hydrous iron oxide imparts yellow colour and the unhydrous red colour. The amount of iron oxide (Fe2O3) in ochre is quite variable. It may be as low as about 20%, going up to 70%. The natural mineral pigment dominates in the market because of its cheapness, abundance in occurrence and good pigmentary quality. Depending upon the colour, the ochres are called red ochre, yellow ochre, green earths, sienna, umber etc.
In addition to red ochre, the red oxide of iron, commonly called 'red oxide', is an important natural pigment. It results from the alteration of hematite and ferruginous laterite and consists essentially of Fe2O3 having pigmentary quality.
Red oxide usually contains about 70% Fe2O3 . Sienna is a brownish yellow containing about 60% Fe2O3 with some quantity of manganese oxide. Due to a huge deposit located in Sienna in Italy it is called as Sienna. Sienna is marketed in the raw and burnt (calcined) states. The colour of the latter is brownish red.
Umber is named after A Central Italy based department first tested Red Ochre so it was name in Umber.Umber is a greenish brown containing some 45% Fe2O3 and 15% MnO2. Umber of good quality, called Turkish Umber, is found on the island of Cyprus. Numerous deposits of colouring earths occur in various parts of the world. Preparation of pigments from red oxide requires an elaborate process. Since it is hard, it has to undergo milling and finally separation of the coarse particles by elutriation.
Ochres being friable are crushed and lixivated, just like china-clay, to obtain extremely fine-textured material of uniform colour. Refining by elutriation followed by drying often improves both iron content and colour.
Application or uses of Ochres: Mainly its use is as tinting colours and for colour washes, distemper and oil paints. It is also used in making coloured paper. For this particular use ochre and china-clay or soapstone, after dissolving in water in paste form, are acreened and added in the beater for the preparation of coloured paper pulp. Red oxide pigments are widely used as primers for painting structural steel, automobile bodies, ship bottoms, etc.
Properties of Ochres: The staining power, brilliance and fineness of texture are the main properties by which an ochre is judged for its quality and value in industry. The tint should be wholly of the inorganic ingredient.
Occurrence in Persian Gulf and Spain : The highest red oxides are found along the Persian Gulf and in Spain. The Persian deposit is mined on the Omur island. A brown oxide found in Pennsylvania, USA, is known as 'metallic brown'.
Pigment Information :Ochre is a natural earth containing silica and clay tinted by hydrous forms of iron oxide, such as yellow-brown limonite or brown-yellow to green-yellow goethite, and traces of gypsum or manganese carbonate. Limonite is a general term used to describe all forms of hydrated iron oxide minerals (FeO(OH)) that occur as natural clay or earth.
Limonite includes the minerals goethite, akaganeite and lepidocrocite. To be considered an ochre, the content of iron oxide must not be less than 12%. Depending upon the content of hydrated iron oxide, the color of ochre varies from light yellow to golden to orange.
The higher the content of iron oxide in an ochre the greater its tinting strength and hiding power. Most yellow ochres are normally not calcined as heat does relatively little to alter their color. Like red iron oxides (hematite), they are found around the world and have been used as pigments since prehistory. French ochre, historically one of the best grades of limonite, contains about 20% iron oxide and is high in silica. In Russia, high quality ochres can be obtained from the Izyumskyy deposit in Ukraine, and the Zhuravskoye, Skarnovskoye and Dubovikovskoye deposits in the Voronezh region, and the Lyubytinskoye deposit near Novgorod.
Oil Absorption and Grinding: Ochre absorbs a medium amount of oil. It slows the drying of oil paint, but forms an excellent film.
Toxicity : Ochre is not considered toxic, but care should be used in handling the dry powder pigment to avoid inhaling the dust.Ochre, Gold :Gold ochre is a natural earth containing clay tinted by hydrated iron oxide, such as yellow-brown limonite or brown-yellow to green-yellow goethite. Ochre, Warm Red :Warm red ochre is a natural earth containing clay tinted by hydrated iron oxide that gives an exceptionally warm orange red hue.